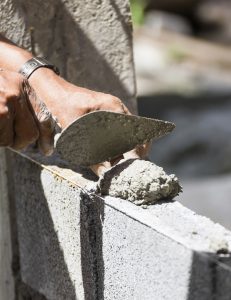
Masonry walls give your building the strength that it needs while also helping to control the temperature inside!
The strongest aspect of a building is its walls. The walls of a building are what keep it standing and give it the strength and durability that it needs. Using masonry materials for walls helps to make them even stronger while also helping to control the temperature inside of the building. Here are some of the different types of masonry walls so that you know which is best for your next construction project.
Load Bearing
These masonry walls are typically made with stone, cement, or concrete blocks. They are made to hold the weight that transfers from the roof to the building’s foundation. Load bearing walls are used for both the interior and exterior of a building and are more economical compared to walls with framed structures.
Hollow
Hollow masonry walls help to keep moisture from getting into the building by putting space between the outside and inside of the wall. The space that is in between the walls keeps heat from getting through the walls, hence helping to better regulate the temperature inside the building. If moisture does get inside the walls, the hollow part will allow it to easily drain downward and out.
Composite
Two or more different units are used to construct composite masonry walls. Typically, a unit is either stone and hollow bricks or bricks with hollow bricks. They take multiple wythes of masonry (a section of masonry that’s one unit in thickness) and bond them together to form the wall. These walls provide a really nice look and are also economical.
Post-Tensioned
These masonry walls are built to withstand very strong forces and weather conditions such as earthquakes and strong winds from tornadoes and hurricanes. Post-tensioned masonry walls have rods that run straight through the core of the masonry units. Once the walls are finished, the rods are then tensioned and attached to the steel that is at the top of the masonry walls.
Contact Del Prete Masonry Today for Your Masonry Walls
If you are ready to upgrade your home or commercial building with professional masonry installation or replacement, Del Prete Masonry has the experience and expertise to get the job done right for the right price. To explore our residential and commercial services and set up a consultation, please give us a call at 410-683-0650 or contact us online. We currently serve Baltimore City and County, Harford County, Carroll County, Anne Arundel County, and Howard County. To see examples of our work and get more updates, follow us on Facebook, Twitter, Google+, and Pinterest.